- Numerical Model of dual frequency induction hardening with finite elements
- Implementation of a material model describing the material behavior (based on results of project B5)
- Thermal analysis with a dilatometer and a short time austenitization test engine
- Induction hardening of gears (42CrMo4) at the transfer partner Robert Bosch GmbH
- Characterization of material state at the surface by optical analysis of the microstructure, measurement of eigenstresses and micro hardness
- ecological and economic balance of dual frequency surface hardening
|
- Implementation in ABAQUS 6.11
- Transfer of the existing material model for 2D-simulation into 3D-simulation
- First steps towards a 3D numerical model of the induction heat treatment of gears
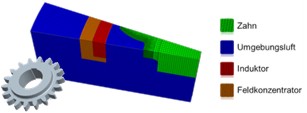
|