- 2D-FE cutting simulation with detailed modeling of friction, heat transfer and phase transformations for the steel 42CrMo4 (AISI4140)
- Turning and drilling experiments with measurement of temperatures and forces
- Abstract modeling of the drilling process (3D-FE model)
- Simulation of phase transformations and work piece distortions
- Defining strategies of compensation
|
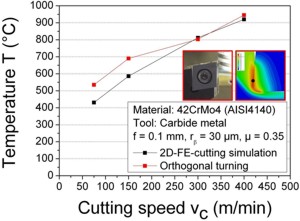 |
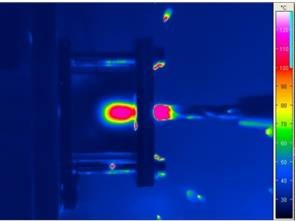 |
Thermal image of drilling experiment |
|
- 2D-FE model shows good agreement of calculated temperatures and forces in relation to the measured results of the turning experiments
- Austenization implemented in cutting simulation
- Friction coefficient decreases with increasing sliding speed and approaches towards a maximum at higher temperatures
|
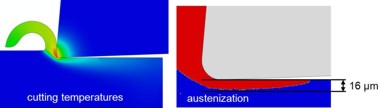 | |